The EU’s Green Deal aims to transform the European economy into a sustainable, climate-neutral and circular, competitive and resilient powerhouse. This vision will be implemented via the EU Chemical Strategy for Sustainability (CSS), the Zero Pollution Action Plan, the Circular Economy Action Plan and other specific policies. There is general agreement that the vision of the EU Green Deal cannot be achieved without a twin green & digital transition of all industries based on new routes to production of chemicals and materials, which provide the needed functionality with improved safety and sustainability profiles. Such so-called Safe-and-Sustainable-by-Design (SSbD) advanced materials and chemicals (AdMas&Chems) will strengthen critical raw materials resilience, decrease energy consumption and greenhouse gas emissions, and support reaching the zero-pollution goal and a toxic-free environment.
To enable industry to develop SSbD AdMas&Chems, the EU funded four projects under the call “Computational models for the development of safe and sustainable by design chemicals and materials” (HORIZON-CL4-2023-RESILIENCE-01-23). The main objectives of these projects are to:
- provide computational models supported by artificial intelligence for the design of new chemicals and materials integrating functionality and the SSbD framework to the chemicals and materials community; and
- boost the innovation capacity of SMEs and industry with cost effective tools to find safe and sustainable alternatives to substances of concern.
PINK, as one of the four funded projects, is addressing these challenges by proposing a tiered approach, which is outlined here.
The EU SSbD Framework
With the development of the SSbD Framework by the EU Joint Research Centre and the release of the Commission Recommendation in December 2022, the EU established voluntary design principles and workflows to guarantee compliance to the highest safety and environmental sustainability standards. The SSbD Framework is based on a hierarchical approach with two high-level components (1st level of hierarchy, see Figure 1), which are executed sequentially in an iterative manner: (i) the (re-)design phase, and (ii) the safety and sustainability assessment phase. This is also called a “stage-gate approach”, where AdMas&Chems are first designed and then they are assessed to determine if they are safe and sustainable.
The assessment phase is based on a defined set of criteria (2nd level of hierarchy) to evaluate the extent of adherence to the SSbD framework. It is composed of 5 steps: Step 1: Hazard assessment of AdMa&Chem; Step 2: Human health and safety aspects in the AdMa&Chem production and processing phase; Step 3: Human health and environmental aspects in the final application phase; Step 4: Environmental sustainability assessment; and Step 5: Scientific basis for the socio-economic sustainability assessment. Even if the word “step” implies a consecutive execution, the EU Framework opens the possibility to run them in parallel. The final (3rd) hierarchy level is selecting and potentially prioritising the specific assessment criteria, also called aspects, for each of the 5 steps.
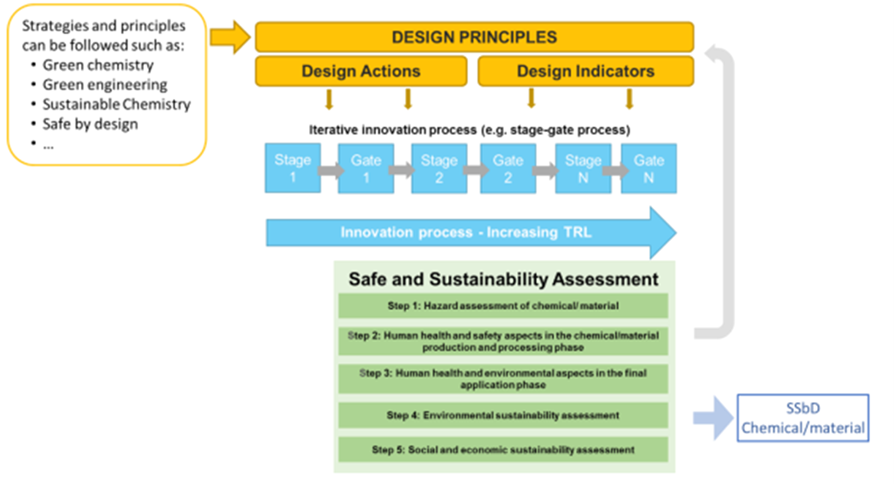
The “D” in SSbD
The idea of SSbD is to integrate these safety and sustainability criteria at the very early stage of the materials development process. In this way, functionality, safety and sustainability are designed into the AdMas&Chems and optimised at the same time. This can also be phrased as the best material performance being defined as the result of a multi-objective optimisation of the “classical” design dimensions functionality and cost efficiency as well as the safety, environmental and social sustainability, and potentially the circularity dimension (see Figure 2).

Replacing experimental evaluation of many or all of the SSbD criteria by computational predictions, especially at early AdMas&Chem development stages, is highly desirable. Use of modelling will limit the negative influence of introducing stricter design criteria on the innovative potential, or may even speed up the material development process, save costs and facilitate in silico testing of new ideas for not-yet-synthesised innovative AdMas&Chems. PINK is currently developing and integrating modelling and simulation approaches to make these available to industry and especially SMEs. Important to note here is that these tools can be quite universal or highly specific for an individual use case (see Figure 3) enforcing a high level of flexibility in the decision support system integrating them.
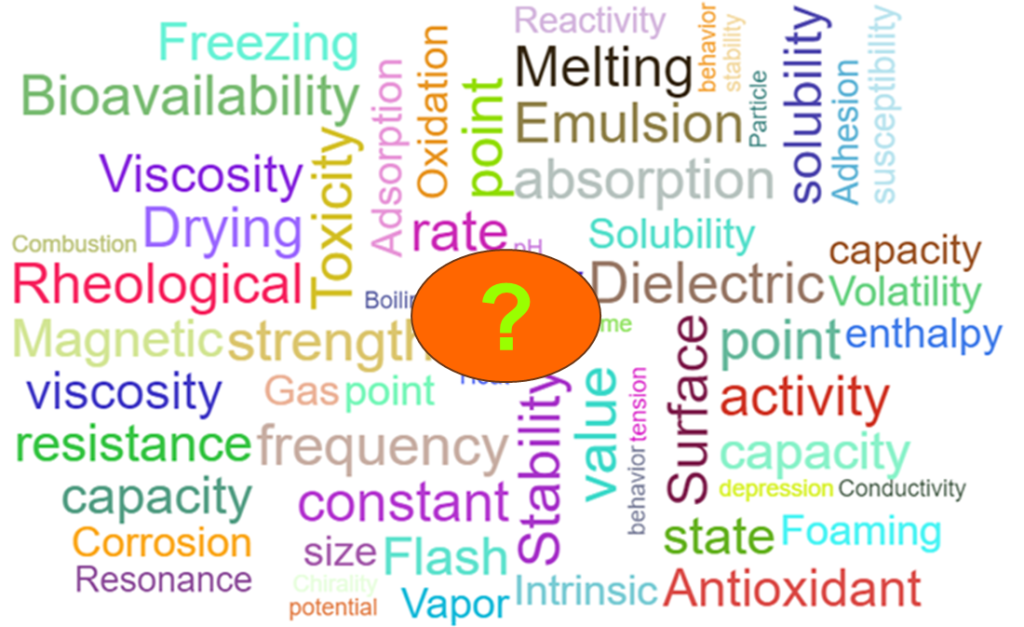
Material life cycle and value chains
In contrast to current regulation, based mainly on the pristine AdMas&Chems, SSbD stresses the need to integrate the full material life cycle and value chains from the raw materials to the different products the material is used in, to their end of life (see Figure 4). PINK is addressing this with a strong focus on exploratory and prospective life cycle assessment procedures to evaluate at the earliest development cycles the environmental impact of introducing a new AdMa&Chem. Additionally, PINK will assess human and environmental impacts during the use phase including unintentional exposure (avoiding chronic aquatic toxicology in one of its case studies) and looking at end-of-life scenarios (biodegradability in the other case study). Additionally, collecting the vast amount of information needed for all the life cycle stages and, in this way, generating a holistic picture of the material’s SSbD performance and of potential sustainability issues, needs to be supported by a system to share technically and semantically interoperable data between up-stream (starting material providers) and down-stream (material and product developers) stakeholders in the value chains. Finally, requirements of specific materials innovation markets, particularities of the selected AdMas&Chems and their use environment (e.g., broad vs. specific applicability domains and/or increased relevance of specific exposure scenarios and toxic endpoints) as well as cross-market harmonisation, knowledge exchange and fertilisation need to be considered and enabled.
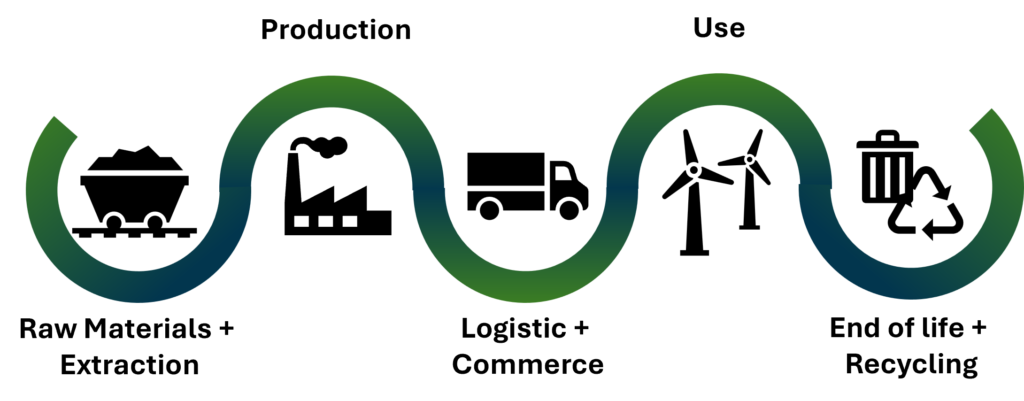
The industrial materials development process
Another aspect to be considered by SSbD is that material development is not a straight line but is an iteratively executed cycle of generation of new evidence and then decision-making on how to progress, i.e. a stage-gate process as the central recommendation of SSbD frameworks from industry associations like Cefic and the EU (see also above). In the best case, the decision at the end of one cycle will enable reduction of the number of candidate AdMas&Chems and the new evidence generated in the next cycle will be useful to further reduce this number and finally end up with the optimally performing material (both with respect to functionality and economic feasibility on the one hand and safety, sustainability and circularity on the other) on the market. Figure 5 shows how this circular process of Figure 2 leads to the confidence to move through these different development phases of industrial material design from business opportunity generation to innovation launch, transforming it into a more or less linear process. In the time between two gates, one cycle is executed with the end being defined by a gate representing the decision to move on with specific candidates and exclude others (lower part of the figure). It also shows the increasing need for data availability and maturity to reduce the chance of failure at later stages according to the “fail early, fail cheap” concept (upper part). However, it is also possible that one has to go back from a later to an earlier development stage to look at new areas of the AdMas&Chems space when the additional information generated in a later step identifies issues with all the selected candidates. This is only implicitly included in the figure since it shows a general direction towards later development stages (arrow to the right) but does not prohibit going back a short distance on this path. For the iterative process, this means that either just another iteration is executed with new candidates added as input or a complete restart of the process is needed if the data for all candidates show that the original design ideas cannot achieve the needed performance.
When implementing the stage-gate approach, informed decisions should be based on the largest amount of data of the best quality that is collectable at that stage with an acceptable effort. At the beginning, almost nothing is known about the candidate AdMas&Chems, especially with regard to safety and sustainability, and they might not even exist as yet (i.e., may never have been produced in a lab). Therefore, the tools provided by PINK for this stage must be able to cover an immense diversity (large applicability domain) of chemistries and must be capable of being run in high-throughput mode. This can only be achieved by making compromises with regard to the level of acceptable uncertainty. In later phases, more complex tools can be applied and experimental data will come in for all SSbD dimensions drastically increasing the certainty of the predictions and decisions based on them.
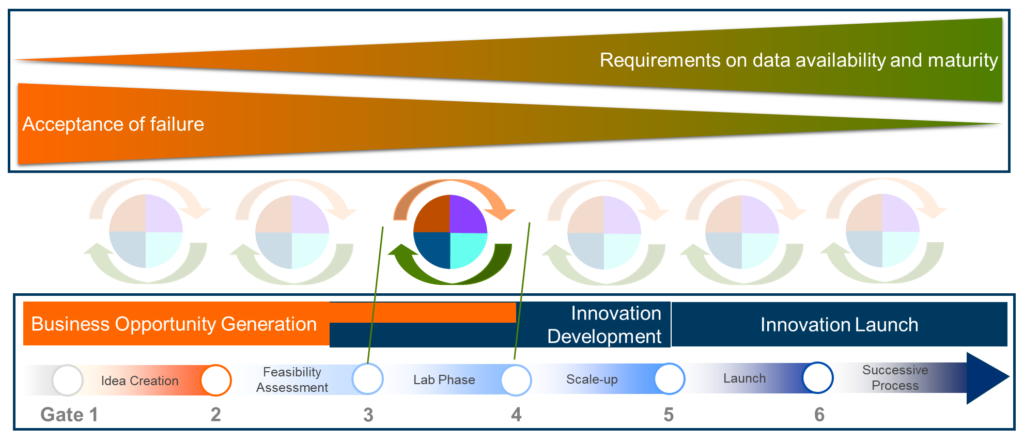
The PINK Matrix of tools vs tiers
All aspects described in the sections above – SSbD dimensions and individual criteria, materials innovation market, material life cycle stage and material development stage – have to be considered when deciding if a computation model or tool is relevant at a specific point of time in the material development campaign. To guide the user, only those tools relevant to the current development stage should be proposed by platforms implementing decision support systems. PINK is creating a tiered approach to provide the right tools at the right time for both the PINKISH platform (PINK’s user interface to the SSbD workflows and decision support, the so-called PINK In Silico Hub) as well as other parallel or future decision support tools, which want to reuse specific PINK tools or evidence from a combination of these tools. This is done on two levels: Firstly, every tool is allocated into one or more tiers according to data requirements, uncertainty, and throughput (tool-based tier levels) and secondly, tools for all SSbD dimensions and life cycle stages fulfilling the requirements of a specific material development stage are made available as input for the multi-objective optimization (scenarios in Figure 6 representing tiers of the materials development process as also used e.g. in the SUNSHINE SSbD support systems developed for nanomaterials).
To make this work, the PINK consortium decided to deviate from the workflow concepts outlined in the EU SSbD Framework in three aspects:
- The strict separation between the (re-)design and the assessment phases will be removed: Selected criteria from the assessment steps defined in the EU SSbD Framework will be evaluated in parallel with functionality and economic viability.
- The workflow will be flexible with respect to the input it accepts: This allows for updated lists of evaluation criteria coming from industry or regulatory guidelines and standards. Integration of parameters from process and product design will be possible. Flexibility to select the criteria and weight them according to the given type of innovation and AdMas&Chems class will be provided.
The use of cut-off criteria stopping further evaluation will only be enforced in later development cycles: In the EU SSbD Framework, reasons for concern from one criterion (e.g., hazard category 1A for carcinogens or even the lack of information about this endpoint) may terminate the process without considering other criteria. However, multiple candidates should be characterised in the early material development stages to understand the influence of chemical and structural variations on functionality and sustainability even if evidence points to safety concerns.
Implementation has started by categorisation of existing tools and those under development in PINK according to their applicability (e.g., SSbD dimension and predicted characterisation/assessment criteria, chemical and material type and innovation market, life cycle stage) and performance (e.g., modelling approach, data requirement, throughput, confidence). This will build the knowledge basis for the tiered approach in what we call the PINK Matrix of tools vs tiers. Currently, this is done manually but one of the first goals of the PINK Semantic Interoperability Framework is to provide this information in a machine-actionable way to facilitate generating the Matrix on-the-fly and customising its components for specific material classes and innovation markets.
We, hence, started to define three scenarios, which represent stages in the material development process, for which we intend to simulate the decision process for the PINK case studies (Figure 6). More information on the Matrix and the scenarios will be published soon.
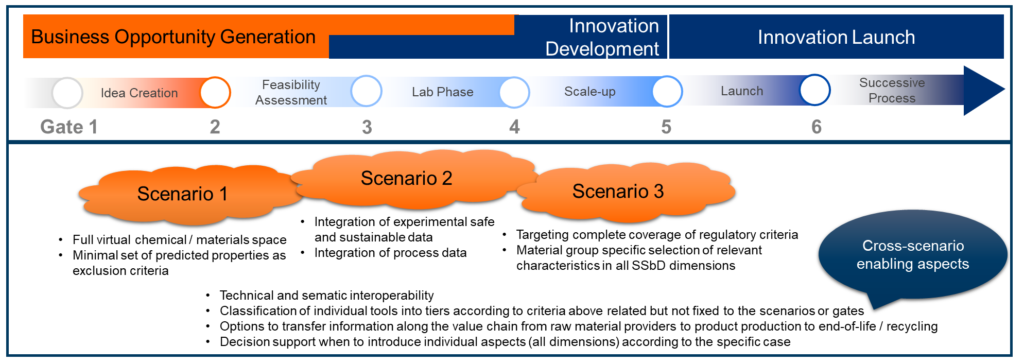